Linda developing materials for future aero engine manufacturing
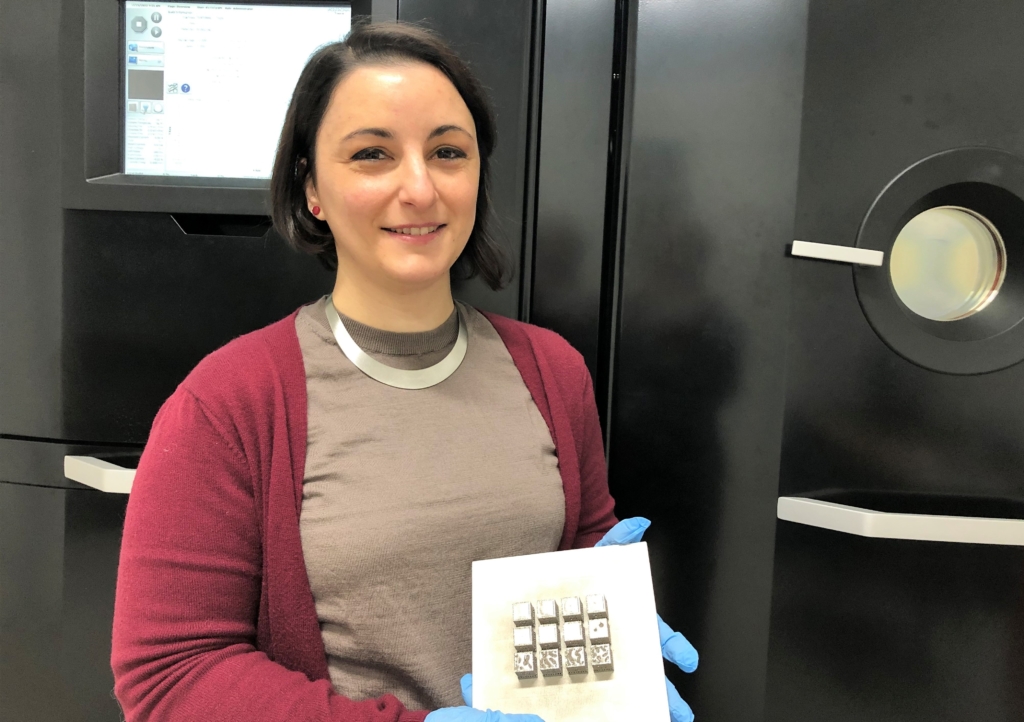
Linda developing materials for future aero engine manufacturing Lighter components, less material and lower costs. These are just some of the benefits that the aerospace industry will gain if they succeed in replacing conventional manufacturing techniques with powder bed additive manufacturing. Doctoral student Linda Squillaci’s research may provide an important piece of the puzzle.
Linda is one of 16 externally employed doctoral students at the industrial graduate school Smart Industry Sweden. She is doing her doctoral studies at University West and is collaborating with several industrial partners, including GKN Aerospace, which manufactures components for aerospace engines.
“Powder bed additive manufacturing (AM) is of great interest to aerospace and other low-volume manufacturing industries. The technology involves building a product layer by layer using a metal powder and, for example, a laser as an energy source,” Linda explains.
The technology is a competitive alternative to traditional techniques such as casting and forging. Powder bed AM manufacturing is more efficient, requires less material and offers lower production costs for smaller batches. Topology optimisation allows lighter components to be made, so the aircraft engine weighs less and requires less fuel.
Enabling smarter design
“This technology can also produce much more complex structures than is possible with conventional techniques. In other words, component design can be smarter,” says Linda.
Linda is part of the PODFAM research project, in which university researchers and industrial partners are collaborating to develop powder bed AM for titanium using lasers as the energy source. The aim is to develop a robust and reliable manufacturing process that meets the stringent quality requirements of the aerospace industry.
“My focus is on developing a basic understanding of how the properties of titanium are affected in this manufacturing technique. Among other things, I’m investigating how different parameters of the manufacturing process affect the properties, microstructure and quality of the material. I’m conducting a range of tests in our lab, for example with different fractions of titanium powder,” says Linda.
“There are many different factors that affect the properties of the metal and it takes a long time to build up understanding and knowledge of each element.”
Network gives insight into other industries
In addition to the practical research work and research studies, Linda has regular meetings and lectures with the other doctoral students who are part of Smart Industry Sweden.
“Being involved in this network is a huge benefit. It’s broadening my horizons in production engineering. I’m learning a lot from the other doctoral students and gaining insights into the industries they work in. It’s clear that we’re all part of the great technological transition that is taking place across industry.”
Linda has extensive experience in mechanical testing, having worked at GKN Aerospace in the UK and Sweden. Her passion for research in materials science has grown over time.
“My goal is to build broad expertise in both metallic materials and mechanical testing.”