How do you get industrial robots to speak the same language?
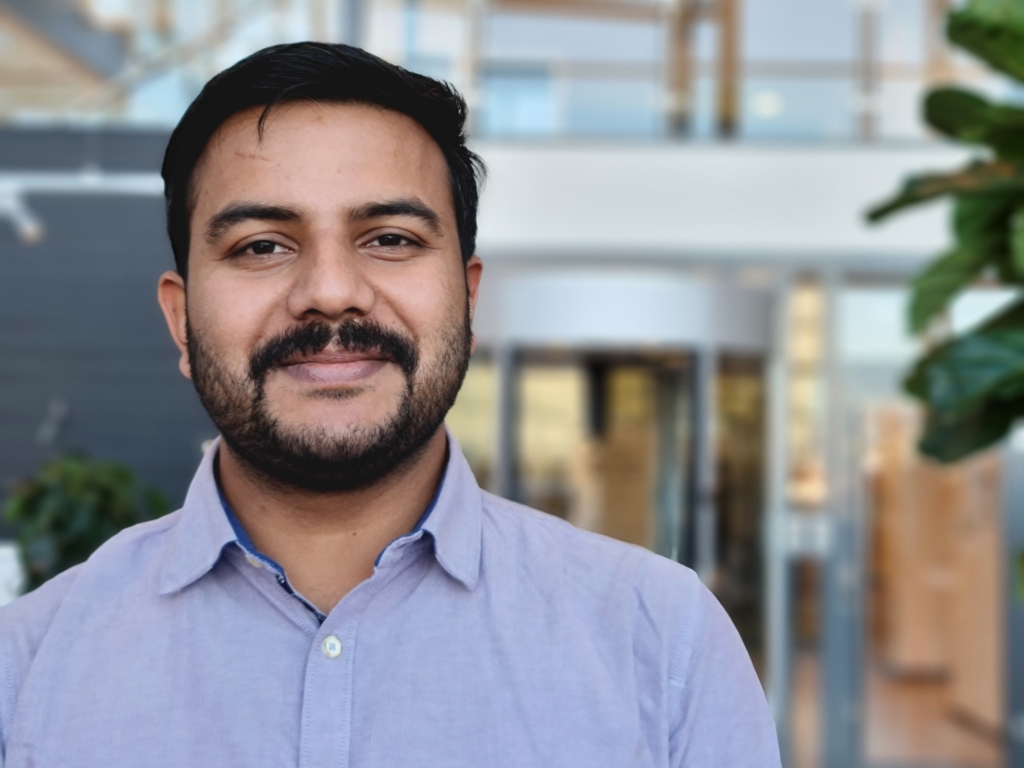
Today, production in the manufacturing industry is complicated by the fact that robots and machines use different information systems and communicate in different ‘languages’. In a collaboration with Volvo Group, doctoral student Gabriel Sebastian’s research is focused on finding a standard that will enable the creation of effective planning tools using digital twins. And these efforts could prove a real boost for flexible production.
A digital twin is a computer model representing something that happens in reality, such as in a machine. Within industry, digital twins are used, for example, to check whether a new production process works as intended before implementation at the factory. Today, the creation of a digital twin requires time-consuming, manual programming. Changes to the production process cannot be made quickly because each such change requires that the model be reprogrammed.
“If, instead, you could create digital twins automatically using the information already found in our robots and other machines, this would be a great advantage,” says Johan Vallhagen, a senior researcher at Volvo Group and Gabriel Sebastian’s supervisor.
“The problem is that the information systems found in different suppliers’ machines are based on unique solutions or different standards, and so they cannot be linked in the necessary manner,” Johan continues.
“With Gabriel’s help, we’d like to accumulate knowledge about which standards and solutions work best together. His research is an important piece of the puzzle for creating tools that can increase the flexibility and robustness of our production, so that we can transition to other product variants more quickly, for example.”
Developing a planning tool
Gabriel began his doctoral studies at University West in March and faces several interesting challenges.
“I’m going to develop a planning tool for flexible production where you use a digital twin for the programming. It must be able to collect and interpret information from several different types of machines regardless of how advanced they are – and it must also be able to include steps performed by production operators,” Gabriel explains.
“This means that we must first create a standard for how digital twins are used for planning in these types of production processes. I’ll apply my research in University West’s newly developed plug-and-produce concept. This is a new form of flexible production where smart modules with configurable tools can be added and removed without any new programming required,” says Gabriel.
Great savings of time and money
If he solves these challenges within a few years, it will be of great significance to companies whose production involves a high level of customisation. A smarter planning tool could mean great savings in terms of both time and money while increasing production reliability and flexibility.
“Here at Volvo Group, it’s a major advantage that Gabriel is conducting his research in close concert with us. It means that our R&D department can accumulate valuable knowledge that we can leverage in several ways, such as when preparing requirement specifications for procuring technical equipment,” says Johan.
Combining doctoral studies with practical applications
Gabriel is looking forward to being able to combine his doctoral studies at University West with practical applications in the production environment at Volvo Group.
“I looked at third cycle programmes where you could work in close collaboration with industry. I consider it important that my research is of relevance to their development work,” says Gabriel.
Gabriel Sebastian is one of University West’s three new externally employed doctoral students. All are a part of the Smart Industry Sweden industrial graduate school, of which another 13 doctoral students from other higher education institutions in Sweden are also a part. Together with 13 industrial companies across Sweden, they are working on industrial development in a number of different technical fields.